There are three types of Inventory. These definitions will help in your efforts to manage inventory and optimize profitability:
- Competitive Items
Available from almost anybody, NAPA parts stores, etc.
- Proprietary Items
Available only from you and your OEM
- Obsolete Items
Dogs. Zero movements in 12 months.
A-B-C-D Inventory Control Still Works
The old approach to classifying inventory by the way items are sold still works. However, we recommend 13 classes instead of 4 because this aids in determining stocking levels. With your computer-aided stock status report, this assessment should be easy.
Steps for Better Inventory Management and Control
- Make sure you have an accurate annual sales history by SKU.
- Generate this report from your Stock Status information:
For each stock keeping unit (SKU) line item, multiply Annual Units Sold by gross profit dollars based on List Price and Cost. List Price less Cost equals the Gross Profit. Units Sold times unit Gross Profit equals Gross Profit Contribution for each line item sold.

- Rank all items in the sequence of Gross Profit Contribution, largest to smallest. The best items with the most gross profit contribution are at the top of the list. At or near Zero profit items are at the bottom.
- Identify “D” or Dead items, those with less than $10.00 gross Profit Contribution for the whole year.
- Remove all D items from this analysis. They are to be handled under a separate disposition program.
- After you remove the D items from the list, classify each remaining SKU into an Inventory Class as shown below.
A-B-C-D Parts Classifications Based on Line Item Gross Profit Contribution
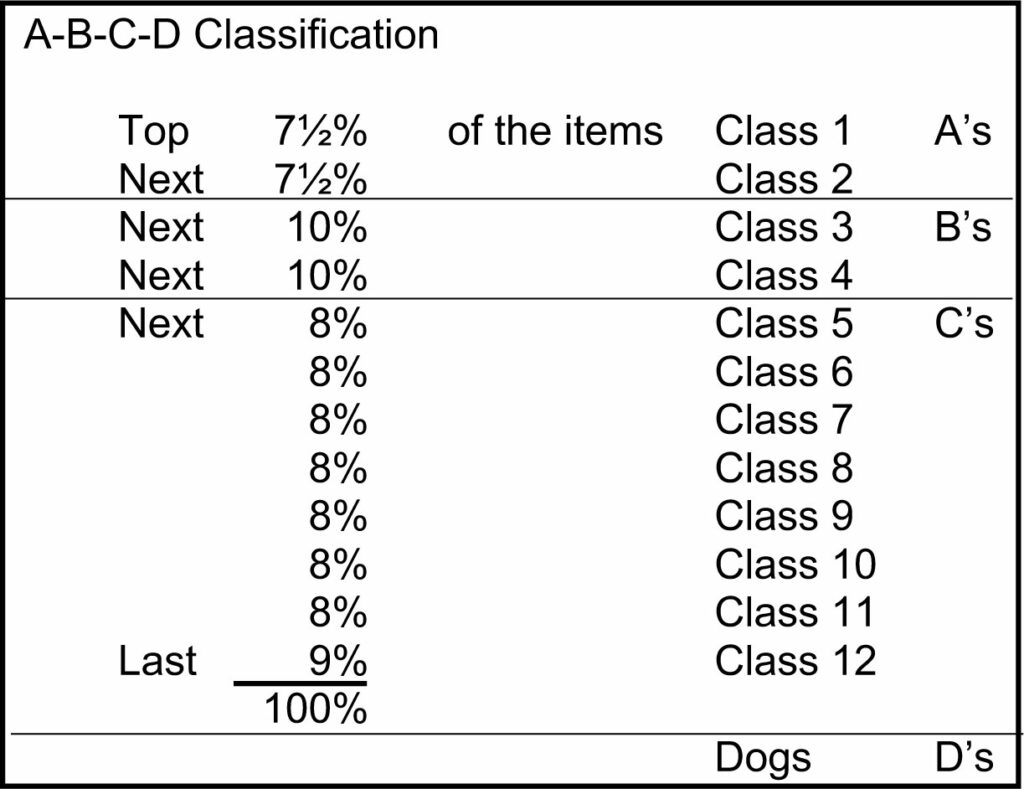
The percentages are the total number of Line Items on the list. For example, if you had 2,500 total line items after taking out “D’s,” Class 1 would have 188 line items. Class 2 would have 188. Class 3 would have 250, etc.
Take into consideration “min-to-bin” time. How long does your vendor take to replenish your stock? Buy no more the Month’s Supply that Corresponds to the Item’s Class. This purchase and replenishment policy is described below.
When it is time to re-order on regular Monthly Stock orders, purchase the amount according to the following chart. There are 12 classes of inventory plus “Dogs” with zero movements.
Maximum SKU Purchase Quantity by Class
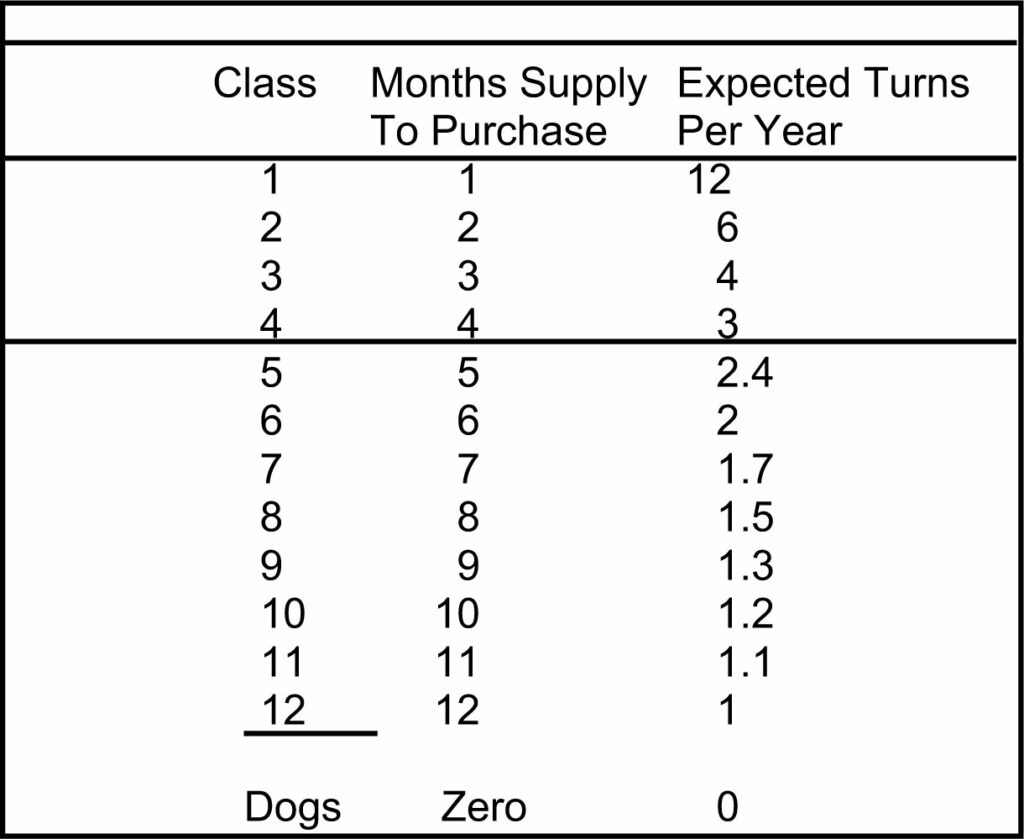
For example, a Class 4 SKU item gets about 3 turns a year so you should probably never purchase and have on hand more than a 4-month supply.
This is an easy way to verify the Economic Order Quantity (EOQ) recommended by your stock status report when the line item is shown at a re-order point.
This is also a way to check for excess stock. Month’s Supply tells you about how many months of inventory you should have on hand by Product Class based on unit turns.
Review Classes 5 through 12.
If you have sold 1 to 6 pieces in 12 months:
Determine which should have a stock level of 1 and re-order point of Zero.
Determine which should have Zero stock and be considered “special order.”
Review Classes 1 through 4.
If you have sold 7 or more pieces in 12 months
Determine maximum months supply to purchase from Maximum SKU Purchase Quantity by Class chart.
What To Do About “D’s,” Your DOGS?
First, make sure there are no “protected items” on your Dog list. These would be items you have in stock to protect new machine models for which you have little or no parts sales history.
For suggestions on how to get rid of Dogs, Dead or Obsolete Stock, see Strategies, Tactics, Operations for Achieving Dealer Excellence, page 234 by Walter J. McDonald. Available under “Books” on this website.